Control of Substances Hazardous to Health (COSHH) Assessments
It is the intention of Ark to secure the health and safety of all people, so far as is reasonably practicable from the hazards in the use, handling, storage, disposal and transportation of all substances hazardous to health, by assessing the risks to prevent or control any ill health effects or accidents arising from or out of any such activities.
The company acknowledges that no substance can be considered completely safe. All reasonable steps will therefore be taken to ensure that all exposure of staff to substances hazardous to health is prevented or at least controlled to within the statutory limits.
It recognises that the co-operation and assistance of all staff is important and that when assessing risks, the recommendations of the staff to substances hazardous to health are prevented or at least controlled to within the statutory limits.
To enable the company to comply with the control of substances hazardous to health regulations it will endeavour to hold all the relevant data on the toxicity and potential hazard of all substances used within the premises. This includes all samples obtained from salespersons.
Each level of management is directly responsible for ensuring that persons within their control are not injured or adversely affected by substances. This will be accomplished by identifying hazardous substances and assessing the associated risks from them together with the processes they are used in or derived from, the implementing of such safety measures to reduce, control or eliminate the risk at source.
Ark has appointed a competent person to complete all control of substances hazardous to health assessments. They are responsible for providing reports to senior management on progress, requirements and problems associated with hazardous substances. They also provide adequate training in the recognition of substance hazards and assessing the risks.
It is the Health & Safety Coordinator’s /Managers responsibility to ensure that contractors visiting the premises, who are required to use hazardous substances, provide copies of their COSHH assessments for the materials they use prior to arrival at site.
Where female members of staff use hazardous substances, it is essential that they report if they are pregnant as soon as possible to ensure any continued exposure, albeit low, will not be hazardous to their health or that of their unborn child.
The Health & Safety Coordinator is responsible for ensuring that their COSHH lists are kept up-to-date and that any changes are notified to the Appointed Person as soon as possible by submitting an amended listing.
A copy of each relevant COSHH risk assessment will be held and a copy will be provided to all those persons considered to be at risk.
Where unsafe practises are detected, individuals are reminded by the management of their responsibilities under the regulations. Where, in the opinion of company management, contractors are using unsafe practises, they are to inform them to cease work until a safer alternative is agreed upon.
The company’s approach to the regulations is to: –
- Familiarise itself with the legal requirements
- Identify and list substances that are used within the company
- Assess the risks to health from working with the substance
- Introduce all of the necessary control measures to safeguard all staff and other persons who may be affected by the company’s undertakings
- Decide what additional precautions may be required
- Implement the precautions that have been decided
- Monitor the precautions that have been implemented and introduce and technique/procedure that would improve safety
All staff have a duty under the COSHH regulations to:-
- Take part in training programmes
- Read container labels
- Practise safe working
- Report any hazard or defect to the management
- Use personal protective equipment provided
- Store equipment and tools properly
- Return all substances to their secure location after use
- Use control measures properly
COSHH Do’s and Do Not’s
Do
- Read the product label and any other information provided so that you understand the hazards of the job before you start work
- Wear the required personal protective clothing and equipment until the job is completed
- Make sure the personal protective equipment is well maintained and fits properly
- Make sure all containers are closed when you are not using them
- Keep your work area clean and tidy
- Clean all spills immediately when they occur
- Follow all instructions on the storage and transportation of chemicals
- Report all accidents or dangerous incidents, however minor
Do Not
- Taste chemicals or touch them with your bare hands
- Try to identify chemicals by their smell
- Smoke or drink in the workplace
- Leave unmarked chemicals around – label as original container
- Be afraid to ask questions
COSHH Assessment Flow Chart
Labelling of Containers
ALL HAZARD WARNING LABELS ARE ORANGE IN COLOUR
Labelling of Chemicals
It is important to ensure that all chemical labelling is clear and concise to ensure that risks to staff are reduced to a minimum.
Containers that are used to hold a temporary preparation need not be labelled, however it is advisable to mark the container in order to determine what is contained within the vessel.
Any container used to store hazardous preparations will be identified with appropriate warning symbols and phrases. Due to lack of space on smaller containers i.e. 125ml or less it may not be possible to write the warning phrases, therefore these may be omitted.
It is a legal requirement to ensure that all chemical substances are correctly labelled (CHIP regs). Therefore any chemical substances delivered not conforming to this will be rejected and returned to the supplier. Guidance on what labelling is required can be obtained from the hazard data sheet supplied with the substance.
Request a Callback
Why Choose Ark?
✔ 1 Hour Response
✔ Fully Accredited
✔ Trained Technicians
✔ Unrivaled Service
✔ CRB Checked
✔ 24hr Callouts
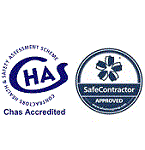
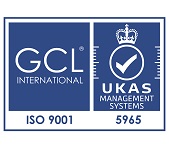
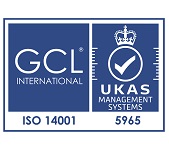
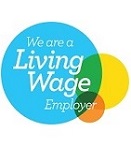
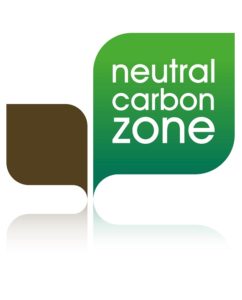
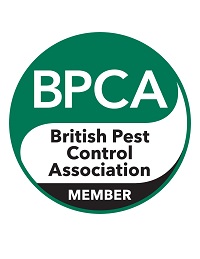